Estimated read time: 4-5 minutes
SALT LAKE CITY — Utah Gov. Spencer Cox spoke two years ago about the need for Utah and the United States to supply its own critical minerals.
"We cannot rely on China and countries in Africa that are controlled mostly by China for our critical minerals. It's a huge mistake," Cox said. "It gives our adversaries far too much leverage. We're already seeing what's happened when we allow someone like Vladimir Putin to be in charge of the energy needs of the world."
That comment was made when Rio Tinto Kennecott announced it was beginning the process of recovering tellurium — one of the rarest elements on Earth — through a $2.9 million circuit built at the Kennecott refinery.
The University of Utah on Monday announced Mike Free and Prashant Sarswat, metallurgical engineers from the school's Department of Materials Science and Engineering, have secured two significant funding awards to advance innovative technologies for rare earth elements and critical metals processing.
"Right now, China is doing 90% of some of these markets, which puts us in a vulnerable position domestically," Free said, echoing Cox's sentiment from two years ago.
To help the U.S. and Utah break into these markets, the Defense Advanced Research Projects Agency has awarded $220,446 for developing refined rare earth elements and critical metals products at 90% purity.
Additionally, the Department of Energy has committed $5 million to support a comprehensive project focused on upgrading mineral resources and optimizing extraction and separation processes to achieve an exceptional 99% purity level for some individual rare earth elements and critical metals products.
The U. is one of only two institutions selected by the Department of Energy in its second funding round — the other is the California Institute of Technology. The project team also includes collaborators from Virginia Tech and industrial partnerships for commercialization.
"We're starting with unconventional resources to build a larger supply chain here in the U.S.," explained Free, principal investigator of the projects. "We are exploring new approaches that are more environmentally friendly. Some of the technologies we're developing, like our magnetic separation process, use no additional chemicals, which are very different from conventional processing that can require hundreds of steps and typically involves substantial amounts of acid."
The U.'s research team — which includes graduate students Easton Sadler and Benjamin Schroeder — will be developing innovative separation techniques, including a unique device that harnesses strong magnets to separate rare earth elements based on their magnetic properties.
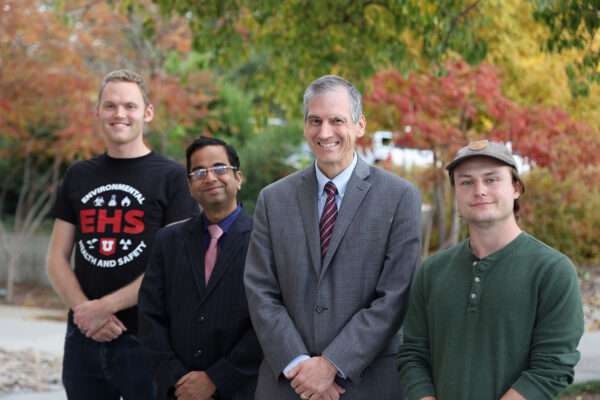
Another project involves exploring new, environmentally friendly extraction methods using specialized materials that can selectively absorb specific elements.
Still, the work being undertaken by the U.'s research team is challenging.
"The properties of rare earth elements are so similar that existing methods and technologies are not very effective at separating them. With our methods, whether it's magnetic or physical separation or adsorption, we can handle that challenge," Sarswat said.
All in all, the research aims to produce:
- Five individually separated, high-purity rare earth oxides/salts at around 90-99.99% purity.
- Five individual or binary rare earth metals at around 99.5-99.8% purity.
- Five additional around 90-99% pure individual critical metals as oxides, salts or metals from coal byproducts.
From the Utah lab, the operational sequence of the purification process extends to collaborators Aaron Noble and Roe-Hoan Yoon at Virginia Tech, who are working with physical separations of rare earth elements and critical metals from unwanted minerals.
Once they enrich the minerals, the U.'s team will dissolve the elements to form ions which go through the magnetic or absorbance processes and further separate the remaining impurities.
Additional processing will then be harnessed to produce high-purity powders, metal oxide minerals and metals. The metal oxide material will move through a conversion process that turns it into metal and this last step will take place in the lab of metallurgical engineering colleagues in the U. Department of Materials Science and Engineering, Zack Fang and Pei Sun, according to a release from the university.
President-elect Donald Trump previously described the Biden administration's signature Inflation Reduction Act as a "green scam" and vowed to repeal it after he returns to the White House in January.
While this signals bad news for electric vehicle and wind power sectors who greatly benefited from the Biden Administration's $369 billion energy transition legislation, Trump seems unlikely to reverse the the U.S. drive to critical metals and rare earth elements self-sufficiency.
In 2020, then-President Trump himself declared the country's "undue reliance" on "foreign adversaries" for critical metals a national emergency.
On the campaign trail, Trump pledged to enact 60% to 100% tariffs on Chinese goods, which would significantly drive up the cost of rare earth elements and critical metals, which are fundamental to modern technologies like electric vehicles, semiconductors, photovoltaic solar panels and electronic devices like cellphones and computers, among a myriad of other things.
But by developing more environmentally friendly extraction methods for rare earth elements and critical metals, the U.'s research team hopes to create a domestic supply chain for such products.
"We're starting with unconventional resources, trying to build a larger supply chain here in the U.S.," Free said. "We want to see the U.S. have more production of these critical things."
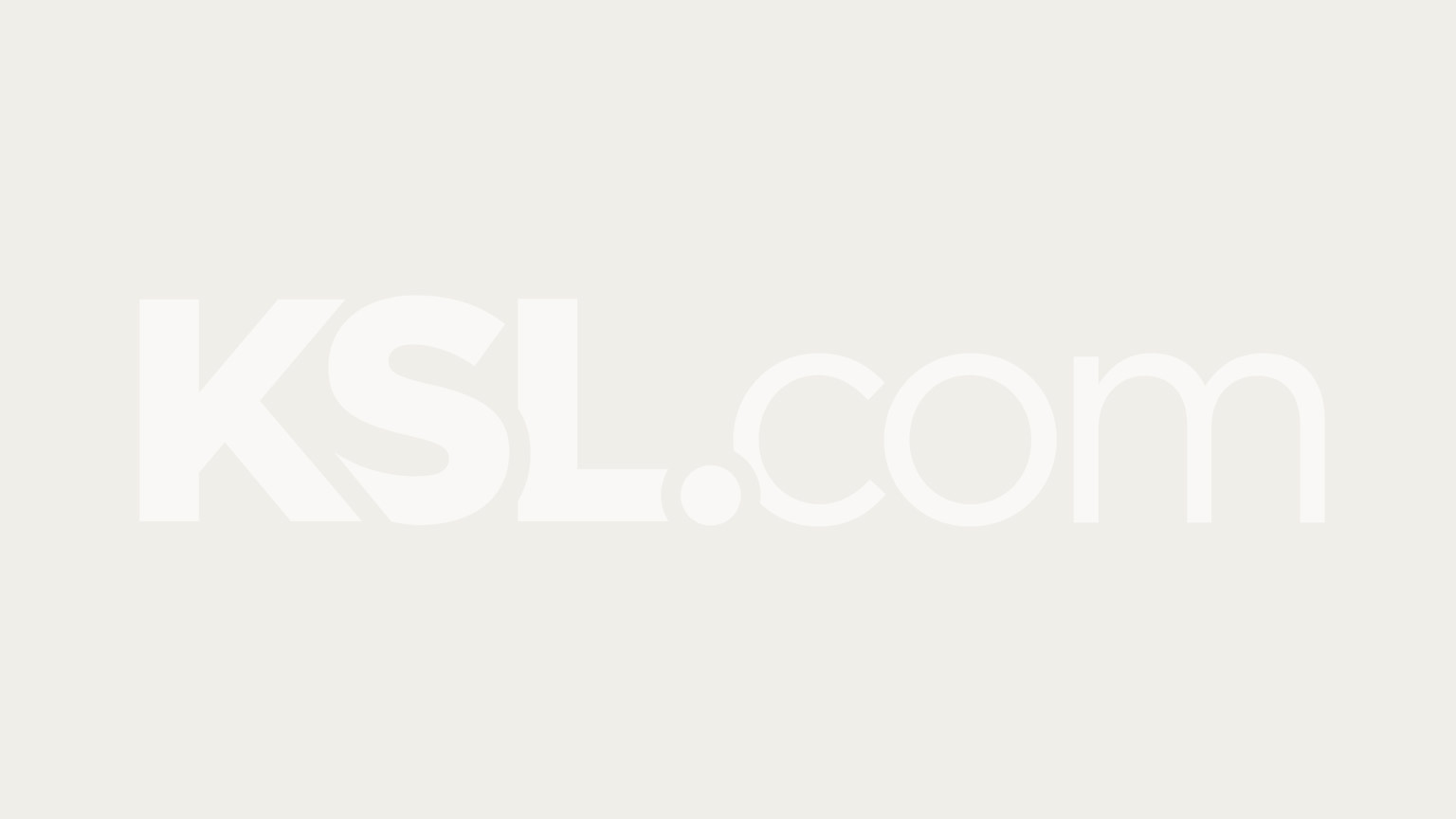