Estimated read time: 3-4 minutes
SALT LAKE CITY — Perhaps it's not the most glamorous detail of building a home, skyscraper or park, but aggregate is one element you can't be without in the construction process.
A broad term, but simply put, construction aggregate is made up of "raw materials that are produced from natural sources and extracted from pits and quarries, including gravel, crushed stone and sand," according to the Association of Equipment Manufacturers.
The average home needs around 400 tons of aggregate when built. A larger building, like a school, takes upward of 15,000 tons.
Last year, "920 million tons of construction sand and gravel valued at $11 billion was produced by an estimated 3,400 companies operating 6,500 pits and over 200 sales and (or) distribution yards in 50 states," the Association of Equipment Manufacturers added.
However, the sources of these materials are not exactly visually appealing — think Geneva Rock products at the Point of the Mountain between Sandy and Lehi.
"I mean, nobody wants these in their backyard. But all of us drive roads to and from, and we're going to need even more material as we build homes and everything else," Rep. Casey Snider, R-Paradise, previously told the Deseret News.
Residents' lack of desire for a quarry or pit near their homes is just one reason, among many, for the gradual price spike in aggregate in recent years.
A report by Twisted Nail LLC found that aggregate pricing increases have varied by state between 2019 and 2022.
States with the most expensive aggregate price increase:
- New Jersey: +41.1%
- Utah: +32.6%
- South Carolina: +32.0%
- Mississippi: +31.7%
- Vermont: +31.1%
Since 2019, Utah's crushed stone prices have increased by 30.3%, and sand and gravel prices have increased by 33.4%.
Dave Kallas, executive director of the Critical Infrastructure Materials Coalition, told Deseret News that Utah has a major depletion problem. "Aggregate pricing and the demand for aggregates is a real economic indicator of the local economy," he said.
Utah has maintained its first-place ranking in the U.S. News and World Report as the best state overall for three years in a row, and its economy and infrastructure ranked third overall. That being said, the increasing demand from the already existing population, added on by the new growth, is then "compounded by the depletion of permitted aggregate reserves."
"We're depleting our resources along the Wasatch Front, so we're having to truck them from even further away. And so those increased transportation and increased hauling are big contributors to the cost in Utah," Kallas added. "We're importing more and more of our material from further and further away."
When the material comes from farther away, transportation costs end up making up the bulk of the overall price.
"While the input costs to produce these aggregates has increased nationwide, an often overlooked driver of cost is the delivery fees associated with bringing these aggregates to their end-use location," Hunter Kosar, of the Texas aggregate supplier Twisted Nail, said, per the study. "These expenses can be as much as 30-70% of the contractor's final cost of material."
Kallas noted that part of the solution to lowering costs includes sourcing aggregate locally rather than importing.
"Aggregates are one of the largest components of construction, and they're produced in Utah and consumed in Utah. From a policy perspective, I think the best thing we can do is have policies that enable local production and keep the production of aggregates as close as possible to the demand."
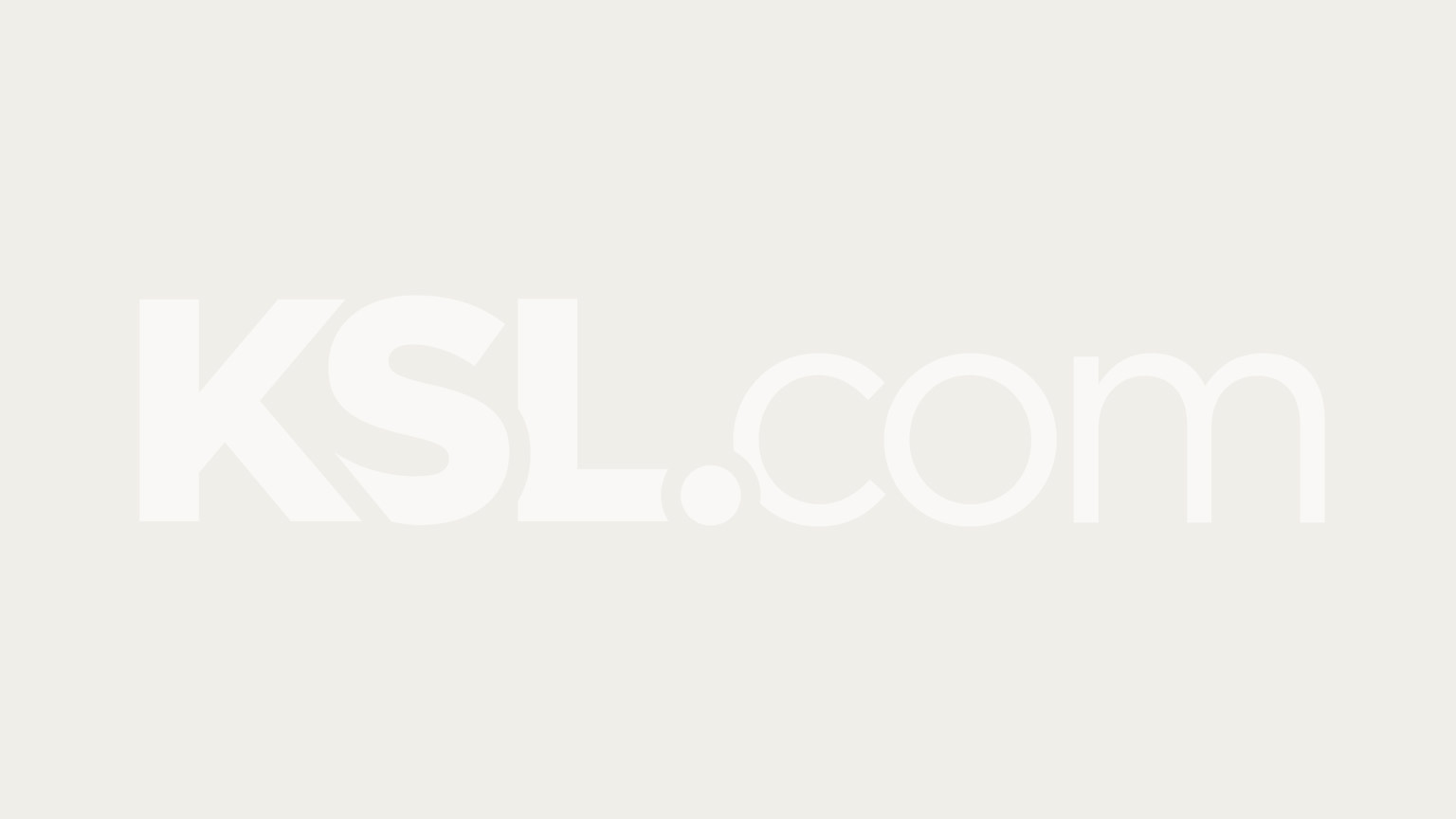